Aluminium as an intelligent part of the solution
"In the future, aluminium shouldn't be part of the global ecological problem, but an intelligent part of the solution," says Arnd Brinkmann, CEO of Gutmann Bausysteme. That's why, as a leading supplier of system-based aluminium solutions for buildings, Gutmann is focusing on a consistently sustainable forward-looking strategy: with efficient recycling management in the production and processing of aluminium - and with recycling-oriented product design for pioneering, Cradle to Cradle-certified façade and window systems.
Aluminium is a fascinating material. For decades, its special properties have inspired engineers to create bold constructions that combine lightness with high strength and resistance – from aircraft and racing car construction to space technology and skyscraper architecture. This is because the light metal, which has only been known for around 200 years and was discovered by the British chemist Sir Humphry Davy in 1808, has a very low density of only around 2.6 to 2.8 grams per cubic centimetre. In addition, it's relatively easy and economical to process, stable, impact-resistant, flexible and also extremely weather-resistant: When it comes into direct contact with oxygen, aluminium forms a resistant oxide layer that protects the material from corrosion and makes aluminium structures extremely durable.
Will aluminium soon be in short supply?
At first glance, aluminium doesn't seem to be a scarce resource: With 8.1% of the earth's crust accounted for by the aluminium ore bauxite, aluminium is the third most common element and the most common metal in the world. A staggering 80 million tonnes are produced annually. But global demand is rising steadily. At the same time, the behemoth China, which has been badly hit by environmental pollution, has considerably reduced the production of its smelters, which cover about half of the world's aluminium demand. The Coronavirus crisis, which disrupted supply chains and shook up the world market and led to a serious shortage and increase in the price of aluminium resources, has made it clear that aluminium could be in danger of becoming a scarce commodity in the future. The shortage on the world market has even prompted some experts to discuss an imminent aluminium crisis. The most recent development, which drastically demonstrates an imminent shortage of aluminium and the accompanying price increase for this valuable resource: The war in Ukraine, which has been raging since the end of February this year and is currently causing the prices of industrial metals to skyrocket. At the end of last year and before the scenario of the Coronavirus pandemic, the World Bank estimated that the price of aluminium would increase by around five percent in 2022. This forecast is already outdated, as the price of aluminium reached record levels in February 2022 and exceeded the 4,000-dollar mark per tonne for the first time. There's almost no end in sight to this development, and it's being fuelled above all by the current situation on the energy markets. Aluminium is rarely found as a pure metal, but usually only in chemical compounds. The extraction processes require a lot of energy – and right now energy is more expensive than ever before. But it isn't just the threat of a shortage of resources and turbulence caused by pandemics and wars that's currently causing problems for the global aluminium market. The climate crisis and current efforts to make the economy as climate-neutral as possible in the future have made aluminium the focus of criticism. This is because the smelter-flow electrolysis process for producing aluminium from the mineral ore bauxite is energy-hungry, and the extraction of bauxite in huge open-cast mines endangers the rainforest in some of the mining countries such as Brazil or India. What's more, aluminium production produces toxic red mud, and its disposal is a serious burden on the ecosystems of the producing regions. These are issues that pose major questions for the future of the global aluminium industry, because one thing is clear despite all the challenges: a future without aluminium would be a worse future. And a phase-out of the valuable light metal is unthinkable for countless sectors from the aviation and mobility industry to mechanical engineering and the construction industry in the coming decades.
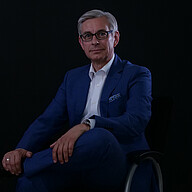
"The generation of this energy is one of the most crucial sustainability issues in aluminium production: in China, for example, where the energy supply is largely based on fossil fuels, around 25 kilograms of CO2 are produced for every kilogram of aluminium produced, while in Norway the figure is only around 0.5 kilograms. Germany currently stands in the middle of the pack, with about 7 kilogrammes of CO2 per kilogramme of aluminium. So nations that get most of their energy from renewable sources are the clear frontrunners here." - Arnd Brinkmann, Managing Director GUTMANN Bausysteme GmbH
Recycling and renewable energies
The good news is that in spite of all the current economic and ecological crisis scenarios, aluminium basically offers a lot of valuable future potential as a clean and sustainable raw material. On the one hand, the high energy demand in aluminium production can be largely mitigated by the use of renewable energies. On the other hand, aluminium is an excellent recycling material that can be reused in modern circulation processes without any loss of quality and with a recycling rate of up to 100% – and with only 5% of the energy required for the primary production of the metal. "One of the most important factors determining the degree of sustainability of aluminium is its origin or the form of energy used for its production" explains Arnd Brinkmann, CEO of Gutmann Bausysteme. "The production of one tonne of primary aluminium requires an average of 15,700 kWh of electrical energy," says Brinkmann.
Cradle to Cradle: product design for future generations
The second important aluminium sustainability issue for Arnd Brinkmann: the use of the valuable light metal in a consistently closed material cycle: "The most sustainable resource is the one that doesn't have to be mined anymore – and recycled aluminium is 95% more energy-efficient than primary aluminium. This is why we at Gutmann Bausysteme operate our own remelting plant on the one hand: here, the aluminium scrap produced in our production is melted down, and subsequent casting produces new high-grade aluminium ingots for the production of our aluminium profiles. We also focus on consistent recycling when it comes to product design. For example, our Gutmann GCW 050/060 façade system doesn't just offer excellent conditions for creative planning and outstanding construction properties. At the same time, with its consistently uniform design, the system is optimised for particularly economical and rational production and carries the Cradle to Cradle certification in bronze. This means: the product already meets key standards of the future in terms of crucial sustainability issues such as material health, material cycle, renewable energies, water cycle and social responsibility."
For Arnd Brinkmann, the Cradle to Cradle principle first conceived around the turn of the millennium by the German chemist Michael Braungart and the US architect William McDonough is one of the most important keys to Gutmann Bausysteme's future sustainability strategy. With Cradle to Cradle, in their book, "Remaking the Way We Make Things", first published in 2002, Braungart and McDonough defined a groundbreaking philosophy of product production that allows only two types of products for a sustainable future: Consumer goods that can be completely biodegraded and consumer durables that can be endlessly recycled without loss of value or quality.
The Gutmann GCW 050/060 façade system, with its Cradle to Cradle Bronze certification, falls into the second category, because its easily dismantled aluminium components are basically designed for an almost infinite life cycle. As it is a "permanent material", the dismantled aluminium elements can be fed into a continuous recycling process; in effect, every aluminium part of the system installed today is also a valuable source of raw materials for tomorrow. "We see aluminium not as part of the global ecological problem in the future, but as an intelligent part of the solution," explains Arnd Brinkmann, "and that's why we're laying an important foundation today for the sustainable architecture of tomorrow with innovative systems like Gutmann GCW 050/060. In Germany, around one third of energy consumption and carbon emissions, as well as more than half of the waste produced, are caused by the construction industry alone. This is why we need to be even more consistent in shouldering our joint responsibility for a sustainable future of construction - because the buildings we construct today will define the environmental future and the living environment of future generations for decades to come."